Lean management voor supply chain
Bij problemen in het productieproces, is de kans groot dat mensen aankomen met lean methode om de problemen op te lossen. De lean methode is ontwikkeld in Japan door Toyota engineers. Deze engineers waren bezig met het verbeteren van toyota productie systeem. Je kan het best een japanse fylosofie noemen. Maar is Lean de oplossing voor alle problemen?
In deze blog vind je de volgende onderwerpen
Bedrijven die serieus met lean werken, merken een positief effect op het personeel en de klanttevredenheid. Lean is in onze ogen meer dan een aantal tools die gebruikt kunnen worden. Lean is een effectief managementsysteem waar de klant centraal staat en het bedrijf werkt hard om waarde creëren voor de klant. Lean word gebruikt als basis voor veel methoden, zoals Demand Driven MRP. In een lean productiesysteem zijn vraag en capaciteit op elkaar afgestemd en werken medewerkers effectief aan het toevoegen van waarde voor de klant.
Oorsprong van Lean management
Het probleem waaruit de lean methodiek is ontwikkelt is terug te voeren op de auto industrie in de jaren 30 van de vorige eeuw. Henry Ford, was aan het begin van de vorige eeuw begonnen met het maken van T-fords. Deze auto was te krijgen in één kleur en één uitvoering. Dit was nodig om de productie zo constant mogelijk te houden en optimaal gebruik te maken van de lopende band. Door het elimineren van variatie en veel handmatige productie kon Henry Ford veel auto's maken tegen een lage prijs. Hiermee bereikte hij het toppunt van Flow, de doorlooptijd van de voorraad was enkele dagen. Dit was in de jaren 30 een heuse revolutie voor de maak processen.
gebrek aan variatie
Het probleem waar Toyota tegenaan liep, was dat hij juist wel variatie wilde in zijn auto's. Het gevolg van de rigide aanpak van Henry Ford, betekende ook dat zijn auto gedurende 19 jaar amper verbeterd of aangepast kon worden.
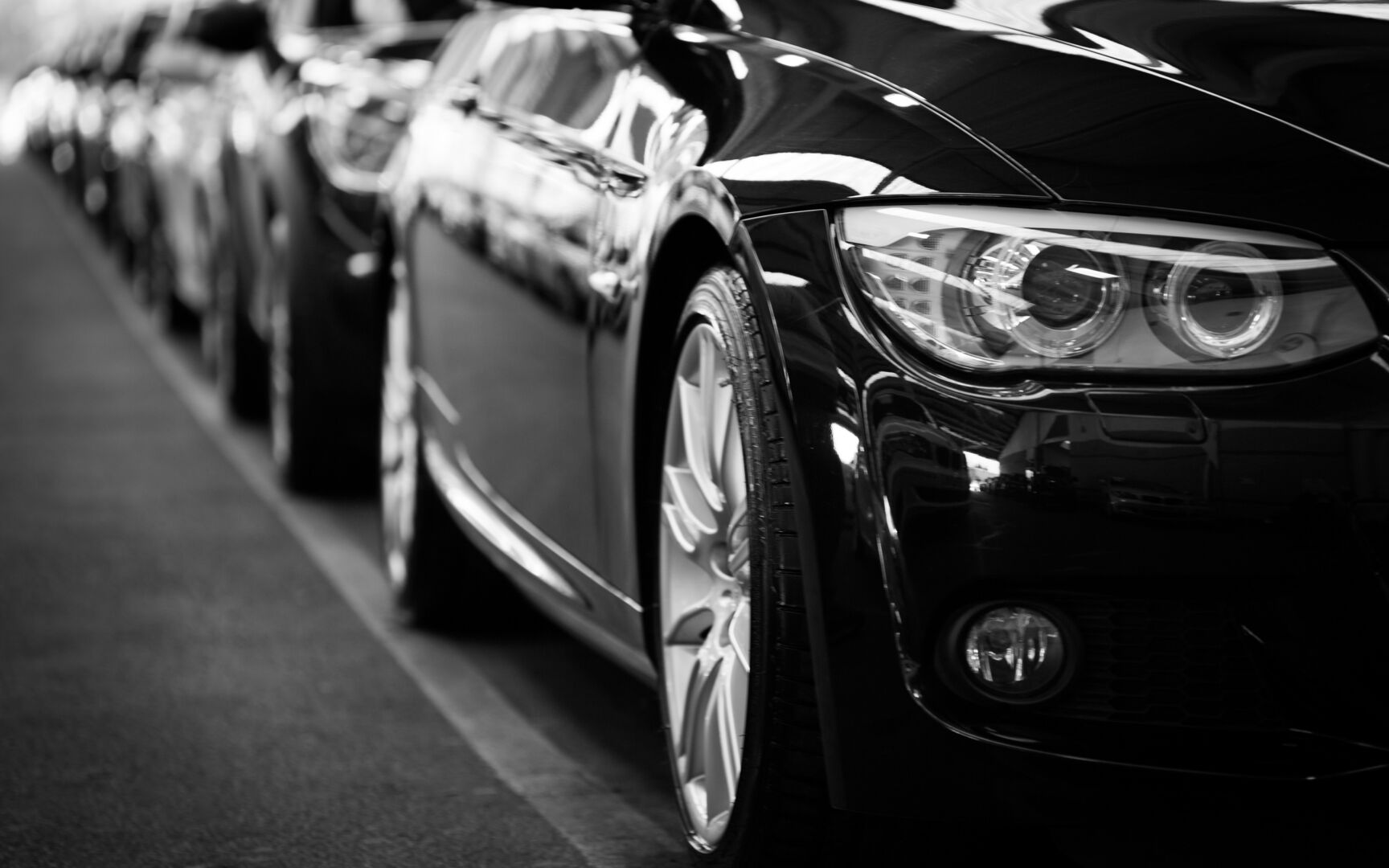
Lean methode
Het systeem waar autofabrikant Toyota aan werkte veranderde de focus van afzonderlijke machines en hun gebruik, naar de stroom van het product door het totale proces. Dit inzicht word wel de start van lean genoemd. Toyota wilde de volgende plannen door voeren in zijn fabrieken:
-
Machines af stemmen op het benodigde volume
-
Zelfcontrole systemen of machines om de kwaliteit te waarborgen
-
De machines in de volgorde van het proces opstellen
-
Korte omsteltijden, zodat elke machine kleine volumes van veel onderdeelnummers kan maken
-
Synchroniseren van processen
Het idee was dat door bovenstaande in te voeren, het mogelijk zou zijn om meer toegevoegde waarde, een hoge variëteit, een hoge kwaliteit en zeer snelle doorlooptijden te leveren naar de klanten. Later is deze aanpak verder ontwikkelt en is bekend geworden als lean.
De vijf lean principes
De belangrijkste vijf principes zijn de samenvatting van de lean methode.
1. Definieer Waarde
Een van de doelen van Lean is om waarde voor de klant toe te voegen. Om dit te kunnen doen, is het nodig om eerst te weten wat waarde voor de klant toevoegd. Welke processtappen helpen de klant en is deze bereid voor te betalen?
De klant staat centraal bij lean en door te verbeteren maak je meer blije klanten, wat het doel is voor iedere organisatie. Het kennen van je klanten en weten waar waarde toevoegen het meeste resultaat heeft, is de uitdaging. Kies je ervoor om snellere levertijden te garanderen of is de klant bereid daarvoor meer te betalen?
2. Breng de waardestroom in kaart
Het tweede Lean principe is het identificeren en in kaart brengen van de waardestroom. In deze stap is het de bedoeling om de waarde van de klant als referentiepunt te gebruiken en alle activiteiten te identificeren die bijdragen tot deze waarden. Activiteiten die geen waarde toevoegen voor de klant zijn verspilling en niet lean.
Verspilling moet zoveel mogelijk voorkomen worden omdat dit geen waarde toevoegd. De verspilling kan worden opgesplitst in twee categorieën: niet waarde toevoegend maar noodzakelijk en niet waarde toevoegend & onnodig. De laatste categorie is pure verspilling en moet worden geëlimineerd, terwijl de eerste zo veel mogelijk moet worden beperkt. Door onnodige processen of stappen te verminderen en te elimineren, kunt u ervoor zorgen dat klanten precies krijgen wat ze willen, terwijl tegelijkertijd de productiekosten van het product of dienst verlaagt.
3. Creëer Flow
Na het verwijderen of verminderen van de verspillingen uit de waardestroom, is de volgende actie ervoor te zorgen dat de stroom van de resterende stappen soepel verloopt zonder onderbrekingen of vertragingen. Flow is de mate waarin de voorraad gebruikt word in efficiënte processen omgaan met de middelen en de voorraad. Een hogere productiviteit met dezelfde voorraad is hogere flow.
De flow kan vergroot worden door het verkleinen van batches en het versnellen van omsteltijden, het opdelen van werk over meerdere workcenters maar ook het opleiden van personeel om zelf de verantwoordelijkheid te krijgen over hun deel van het productieproces.
4. Zorg voor Pull
Voorraad wordt beschouwd als een van de verspillingen in elk lean productiesysteem. Het doel van een pull-gebaseerd systeem is de voorraad en work in process (WIP) items te beperken en er tegelijk voor te zorgen dat de nodige materialen en informatie beschikbaar zijn voor een vlotte doorstroming van het werk. Just-in-time levering en productie mogelijk, waarbij producten worden gemaakt op het moment dat ze nodig zijn en in precies de hoeveelheden die nodig zijn. Pull-gebaseerde systemen worden altijd gecreëerd vanuit de behoeften van de eindklanten. Door de waardestroom te volgen en achterwaarts door het productiesysteem te werken, kunt u ervoor zorgen dat de geproduceerde producten in staat zullen zijn om aan de behoeften van de klanten te voldoen.
5. Streef Perfectie na
Verspillingen worden voorkomen door het bereiken van de eerste vier stappen: 1) het identificeren van waarde, 2) het in kaart brengen van de waardestroom, 3) het creëren van flow, en 4) het invoeren van een pull-systeem. Echter, de vijfde stap, het nastreven van perfectie, is de belangrijkste van allemaal. Het maakt van Lean thinking en manier van continu verbeteren een onderdeel van de organisatiecultuur. Elke werknemer moet streven naar perfectie bij het leveren van producten op basis van de behoeften van de klant. de meeste bedrijven moeten een lean transformatie ondergaan voor ze pas als echte lean organisatie aan de slag kunnen. Het doel is om elke dag een stukje beter te worden.
De principes toepassen
De vijf Lean principes bieden een kader voor het creëren van een efficiënte en effectieve organisatie. Lean stelt managers in staat om continu verbeteren in hun organisatie te organiseren en te ontdekken hoe klanten beter bedient kunnen worden. De principes stimuleren het creëren van een betere flow in werkprocessen, slimmer werken en het ontwikkelen van een continue verbetercultuur. Door alle 5 principes toe te passen, kan een organisatie concurrerend blijven, de waarde die aan de klanten wordt geleverd verhogen, de kosten om zaken te doen verlagen en hun winstgevendheid verhogen.
Lean six sigma
Lean Six Sigma is de combinatie van twee methodes om te verbeteren. Vanuit Lean wordt er gewerkt aan flow en het toevoegen van waarde, terwijl Six Sigma een projectmatige aanpak met kwantitatieve analyses verzorgt.
6σ is de officiele schrijfwijze
six sigma staat voor een klein getal, namelijk 99.99966%. De bedoeling van Six sigma is dat de processen zo goed gecontroleerd worden, dat six sigma van de producten goed uit het maak proces komen en bij de klant worden geleverd. Voor de meeste bedrijven is het een streven die ze graag willen behalen.
verbeter traject
Lean Six Sigma maakt gebruik van de DMAIC structuur die zijn oorsprong kent vanuit Six Sigma. Volgens DMAIC wordt een project opgedeeld in verschillende fases: Define, Measure, Analyze, Improve en Control. Dit zijn de stappen die worden genomen om een lean six sigma project uit te voeren.
-
In de eerste fase wordt het huidige proces beschreven en vastgesteld wat onderzocht gaat worden
-
In de tweede fase worden metingen verricht, hoe werkt het process, wat zijn de variabelen en deze worden vervolgens gemeten.
-
In de derde fase worden de metingen geanalyseerd, waarom bevat deze batch fouten, wat voor invloed heeft daarvoor gezorgd?
-
In de vierde fase worden huidige processen aangepast om een oplossing te implementeren.
-
In de vijfde en laaste fase word gekeken hoe de nieuwe werkwijze of verandering "onderhouden" kan worden, zodat het gevonden probleem zich niet opnieuw voordoet.
black, yellow of green belt
Lean six sigma projecten worden uitgevoerd door mensen die daar speciaal voor worden opgeleid. Hoe ver iemand is met lean six sigma, word aangeduid met kleurcodes uit de judo wereld. De begeleiding gebeurt door een master black belt, deze begeleid projecten en helpt mensen om zelf hun black, yellow of green belt te behalen door het uitvoeren van projecten.
Tips voor implementatie Lean methodiek
veel bedrijven willen tegenwoordig lean zijn, lean werken en de term lean word vaak gebruikt om aan te geven dat een bedrijf, flexibel omgaat met de vraag en de klantwaarde goed in beeld heeft. Wanneer je naar een autofabriek van toyota in Japan gaat en vraagt, hoe lean zijn jullie? dan zal het antwoord je verbazen. Lean draait namelijk niet om het worden van lean, of iedereen leren wat de lean methode is. Bedrijven die ver zijn in de lean management methode zijn continu bezig om verder te komen, verspillingen te minimaliseren en op zoek naar mogelijkheden om waarde te creëren voor hun klanten. Zodra bedrijven bezig blijven met lean is het een effectief managementsysteem om maximale toegevoegde waarde voor de klant te realiseren. Lean is geen hype, lean werken is niet iets wat het management beslist. Lean gaan werken vraagt de benodigde investeringen van het personeel en vereist continue aandacht, ook jaren na invoering.
Wil je meer weten over lean, of met ons sparren over de mogelijkheden om bedrijfsprocessen te optimaliseren? neem gerust contact met ons op om te kijken naar de mogelijkheden!